Clementine is an inexpensive, rugged handheld device for administering newborn hearing screening, designed for use in developing countries. I worked as a design engineer in a team of 8 graduate students from Rhode Island School of Design, MIT Mechanical Engineering, and MIT Sloan Business School to develop Clementine’s concept, form factor, and business model.
Our team moved from in-person meetings to virtual Zoom sessions mid-semester due to COVID-19, resulting in difficulties developing an alpha prototype. The project culminated in two separate prototypes: a “works-like” electronics system using an Arduino processor and a 3D-printed “looks-like” prototype.
We started by BENCH-MARKING similar products and surveying stakeholders
We spoke with pediatricians, audiologists, parents, NGOs, and design consultants to gather qualitative data about existing hearing screening devices. For each stakeholder, I wrote a discussion guide for our team centered around learning objectives with questions designed to probe for relevant information.
From our research we identified several pain points with existing devices, along with a set of criteria to guide our design process moving forward. Due to COVID-19, we were unable to contact as many stakeholders as we wanted in this initial research phase, so we continued to conduct interviews and shape our criteria throughout the semester.
based off our research, we brainstormed new solutions,

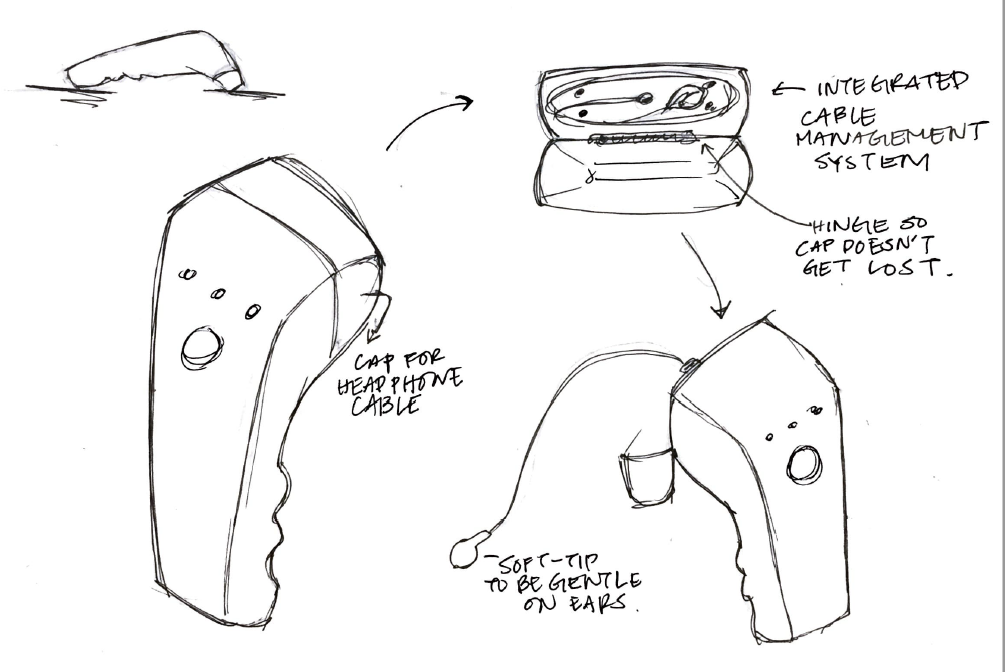
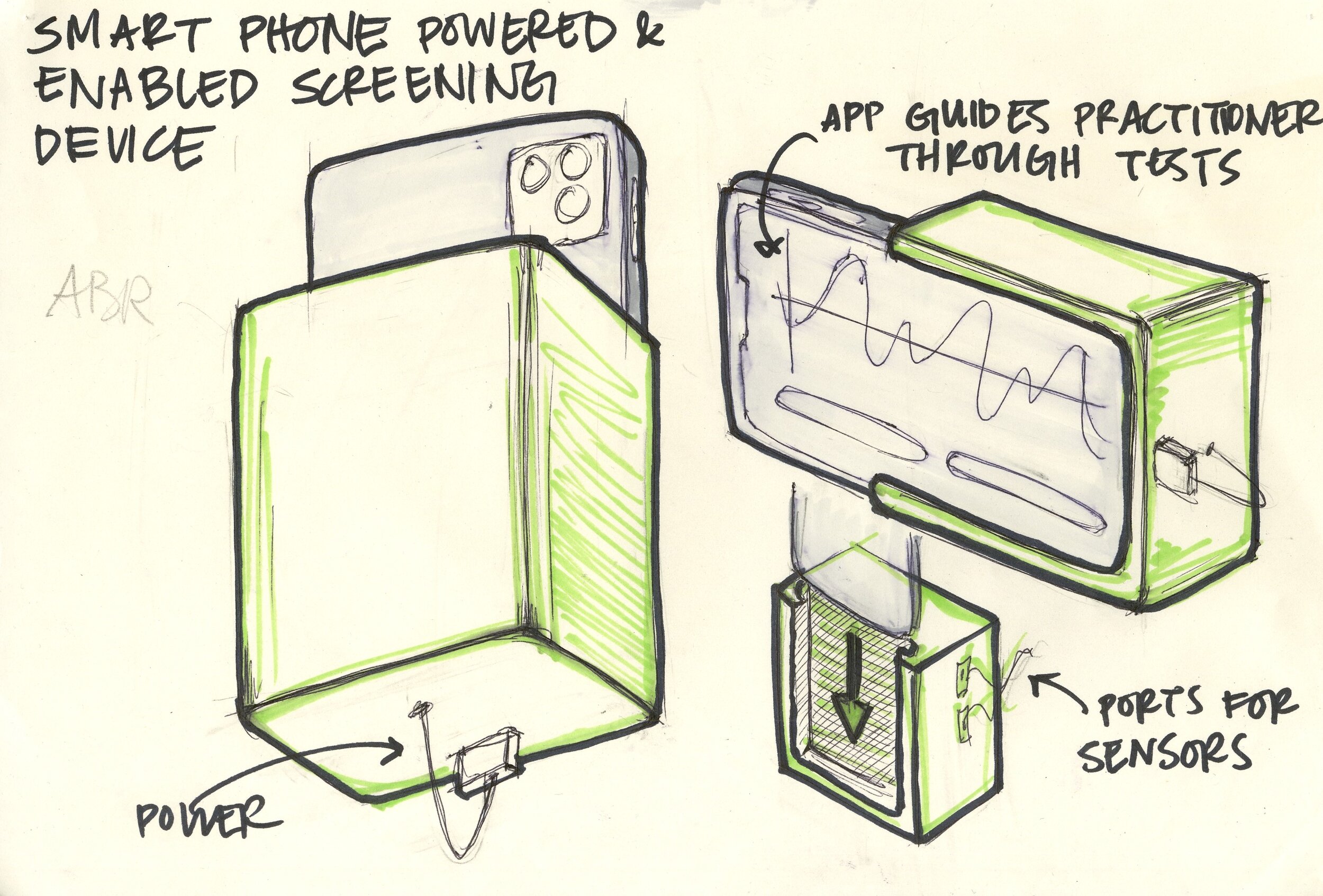
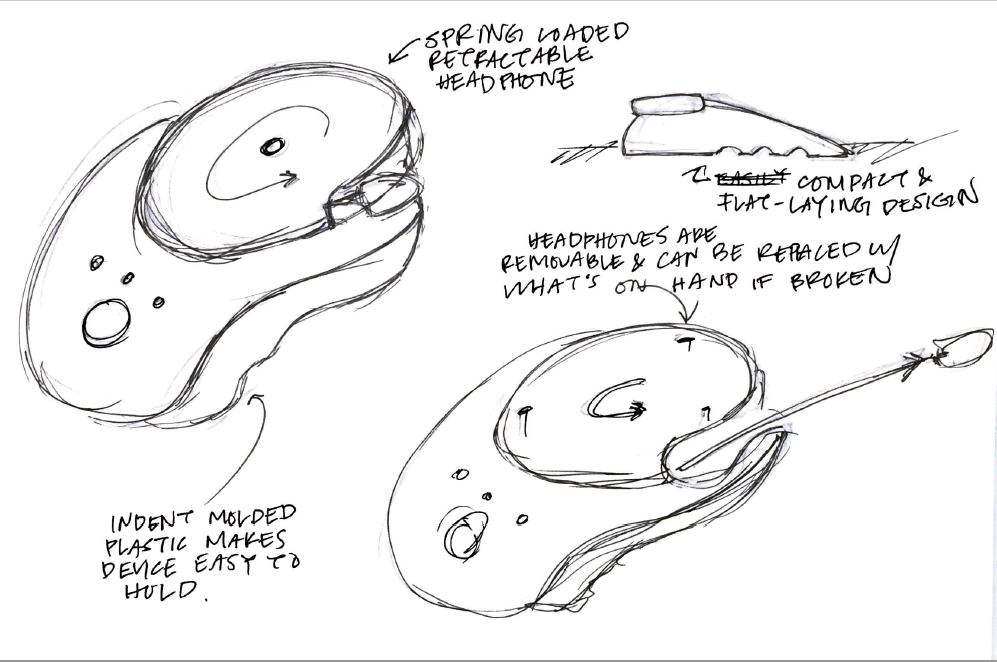
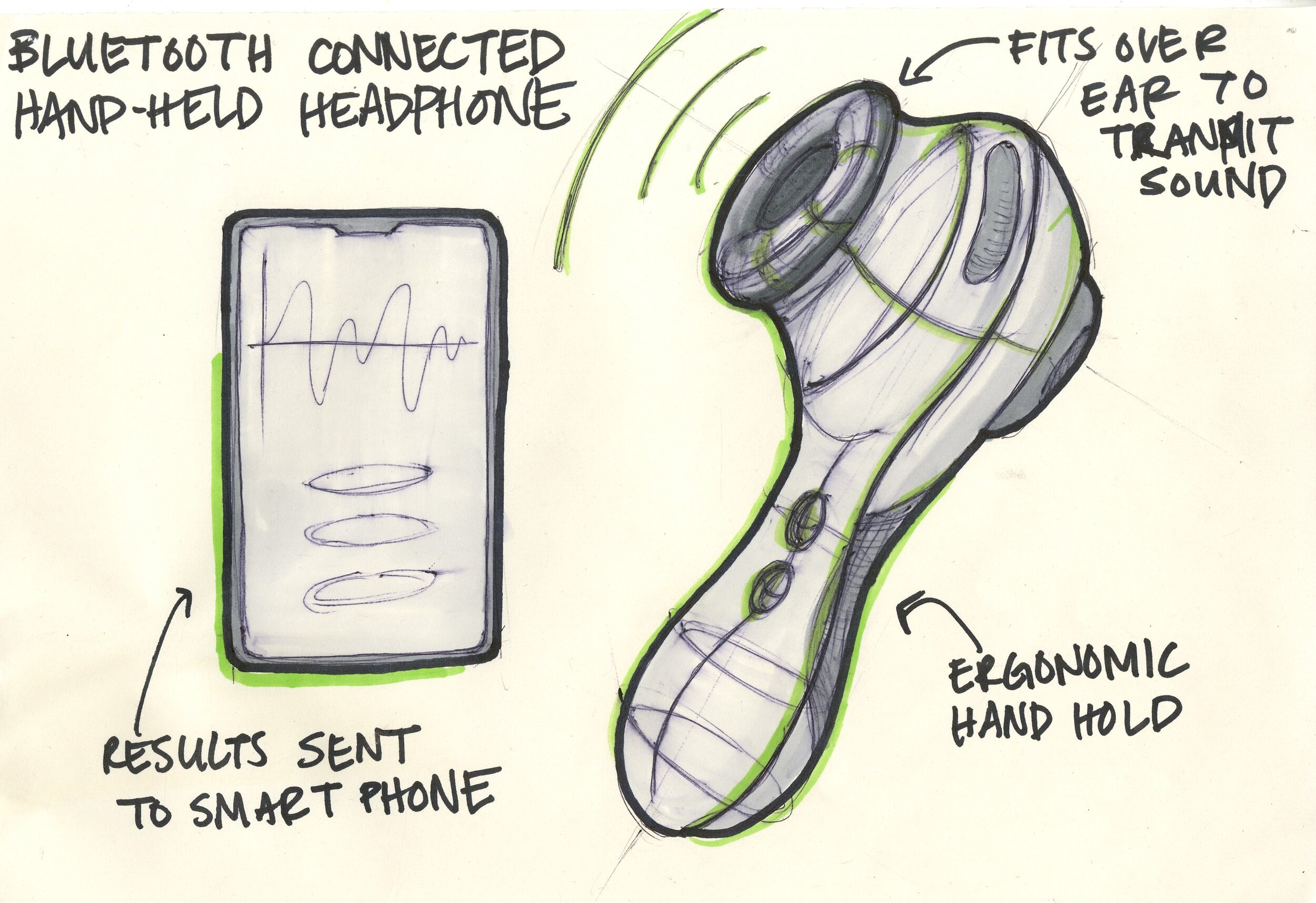
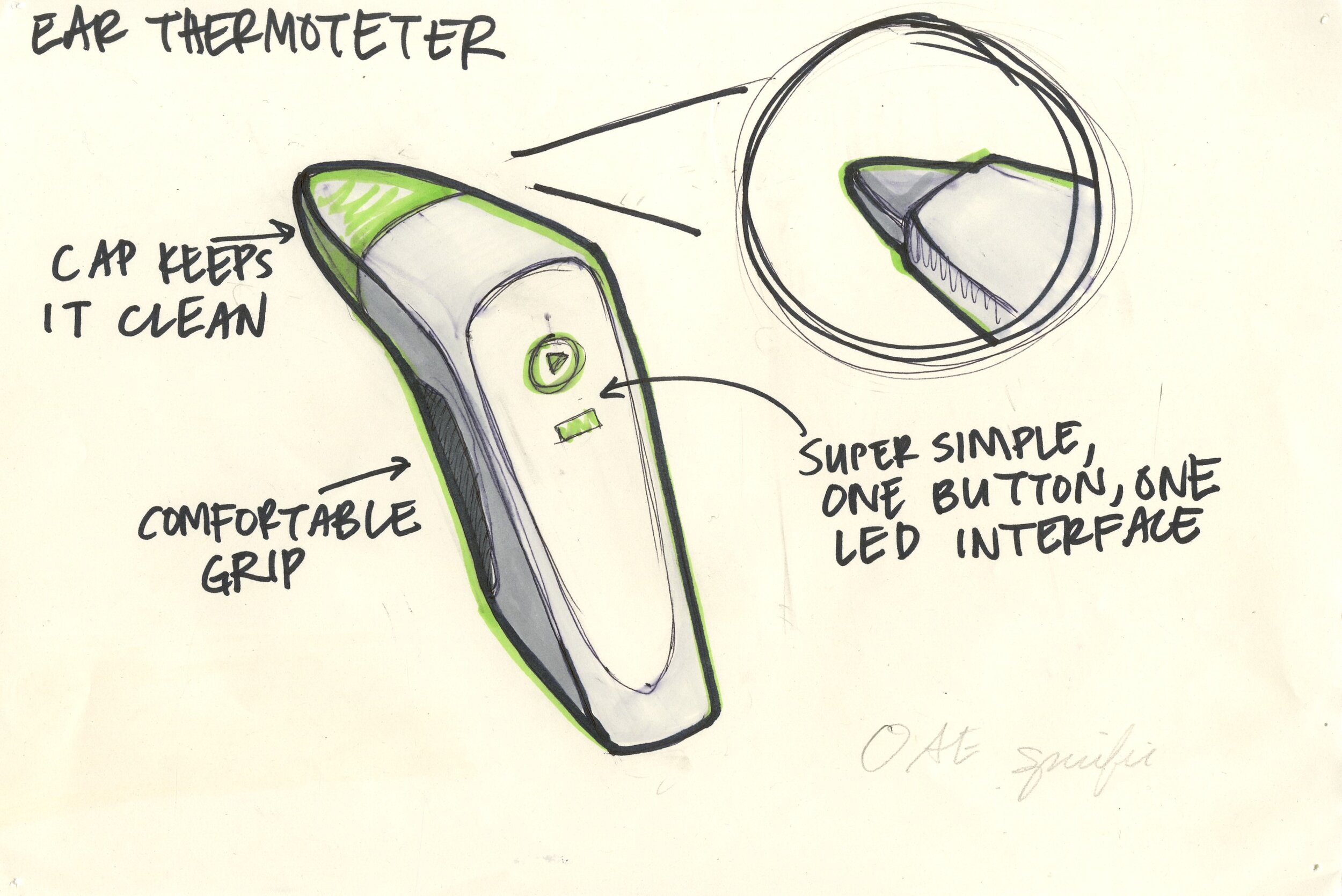
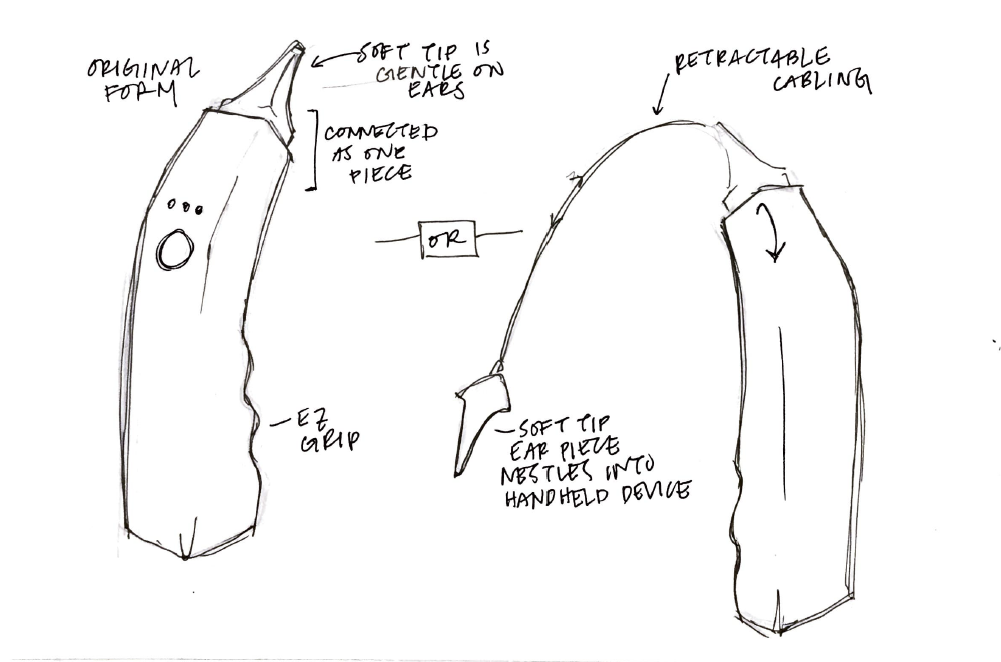
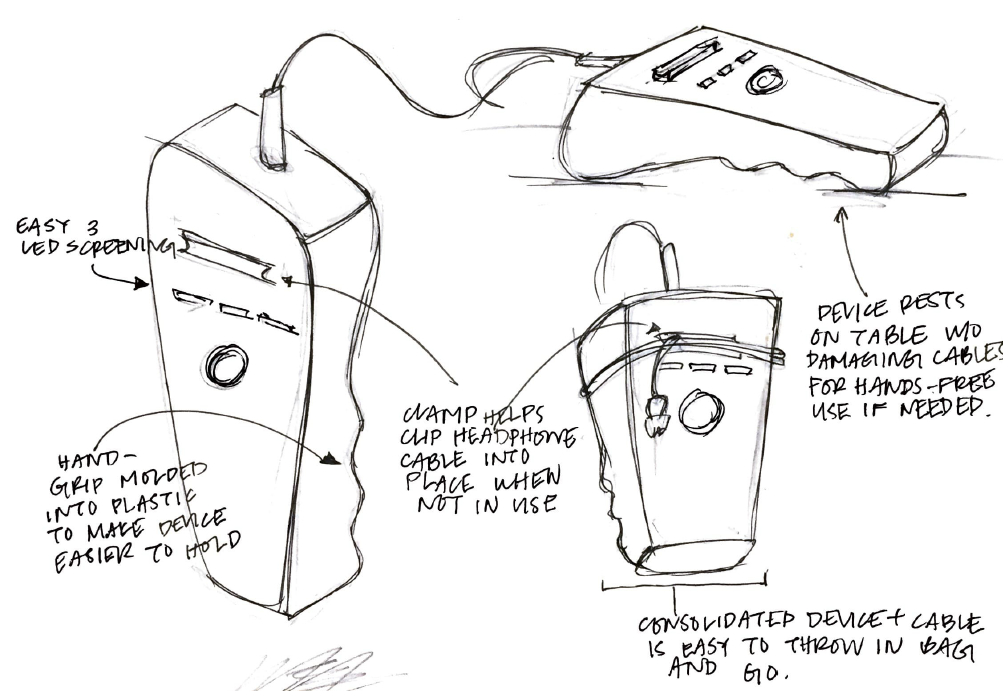
As a group we brainstormed several different solutions, ranging from wearable devices to mobile applications. We decided that handheld “self contained” devices best fit our design criteria and continued digging deeper into that category. I was responsible for sketching a variety of corded and cord-less designs for our final concept selection.
created low fidelity prototypes,
and selected our final concept.
I was responsible for MODELING, iteration, and design for manufacturing
Our team’s primary mode of manufacturing was through STL printing, and all the below designs were modeled for 3D printing.
Our first model was a solid body part with an ergonomic handle and a tip based off otoscope tips for newborns.
I hollowed out the solid body to allow space for the internal battery and processing board. This 2 part body would later evolve to a curved split that allowed easy access to the otoscope tip
Based on user feedback from an audiologist familiar with medical device design for the developing world, we created iterations of our handle shape: our stakeholder expressed that the device needed to be easier to hold (harder to drop) and that we should design for smaller hands, as most practitioners administering these tests would be women. From this information, we decided to add a flange at the bottom of our handle and ridges for more grip.
We also received feedback that a plastic tip could potentially damage a newborn’s ear if they happened to move during the test. In response, I added grooves to the ototscope tip to allow for a silicone covering.
Initial handle shape
Handle with flange
Smaller handle with flange
Finally, I integrated the internal parts for a complete assembly.